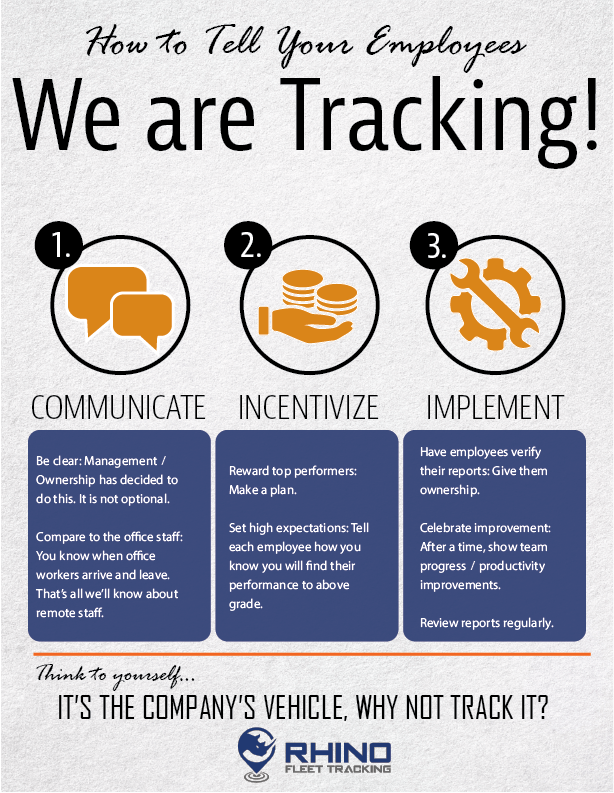
Tracking repair history for your business vehicle fleet is essential for efficient operation and cost management. Imagine a scenario where you can anticipate potential breakdowns and maximize maintenance schedules, leading to significant cost savings and improved fleet performance. This thorough guide explores the crucial steps to effectively track repair history, ensuring your vehicles are always running smoothly and minimizing downtime. This article will cover the importance of repair history tracking, various methods for implementing a robust system, and practical strategies for maximizing the benefits. We’ll delve into practical examples and suggest tools that will aid you in this process.
Understanding the Importance of Repair History Tracking
Why Track Vehicle Repair History?
Tracking vehicle repair history is more than just record-keeping; it’s a strategic investment in the longevity and profitability of your fleet. Accurate records offer invaluable data to maximize maintenance schedules, predict potential issues, and ultimately minimize downtime. By analyzing repair trends, you can determine recurring problems, anticipate future expenses, and make informed decisions about preventative maintenance.
Establishing a Robust Repair Tracking System
Choosing the Right Tools and Technologies
selecting appropriate tools and technologies is paramount for effective repair history tracking. A dedicated software solution can centralize all repair records, enabling real-time access for authorized personnel. These platforms often offer attributes like automated reporting, maintenance scheduling, and real-time diagnostic information, boosting efficiency and improving decision-making.
Related Post : Ensuring Quality Workmanship on Company Vehicle Repairs.
Implementing and Maintaining the System
Training and Communication
Effective implementation hinges on thorough training for all pertinent personnel. Clear communication channels are crucial for ensuring accurate and consistent data entry. Explain the importance of the system and the value of the data it generates to promote active participation from all involved.
Analyzing and Using the Data for Decision Making
determine Patterns and Trends
Detailed examination of repair history data reveals patterns and trends in vehicle maintenance needs. By studying this information, you can create preventative maintenance schedules and allocate resources strategically to reduce unexpected breakdowns. This strategic approach can lead to cost savings by reducing unplanned maintenance expenses.
Utilizing Data for Preventative Maintenance
Proactive Maintenance Schedules
This proactive approach, powered by historical data, allows for more efficient maintenance scheduling. Preventative maintenance procedures can extend the lifespan of vehicles, reduce the frequency of unexpected repairs, and mitigate the occurrence of catastrophic failures. The objective is to shift from reactive maintenance to predictive and proactive measures.
Additional Tips and optimal Practices
Implementing a Standard Operating Procedure (SOP)
An SOP for documenting repairs ensures consistency in the process and the quality of the information collected. This involves standardizing forms and procedures for recording repairs, ensuring accurate data entry and improving examination accuracy.
Case Study: A Trucking Company’s achievement
Optimizing Fleet Maintenance
John Smith, owner of Smith Trucking Company, saw a 15% reduction in repair costs after implementing a robust repair history tracking system. The system allowed Smith to determine recurring issues with a specific tire model, enabling him to proactively address the problem, preventing further expense. This example demonstrates the practical application and tangible benefits of effective vehicle repair history management.
Integrating with Other Systems
Streamlining Operations
Integrating repair tracking software with other fleet management systems, such as GPS tracking, can offer a holistic view of vehicle performance. This integration allows for thorough data examination, leading to improved decision making and reduced maintenance costs.
Future Trends in Fleet Maintenance
Utilizing Artificial Intelligence
Artificial intelligence (AI) will play a growing function in predicting maintenance needs based on historical data and real-time sensor data from vehicles. This approach enhances predictive maintenance and minimizes unplanned downtime significantly. The objective is to move from reactive to preventative maintenance in order to boost efficiency and improve profitability.
In conclusion, meticulously tracking repair history for your business vehicle fleet is crucial for optimizing maintenance, reducing downtime, and maximizing ROI. By implementing a robust system, you’ll gain valuable insights into vehicle performance, anticipate potential issues, and make data-driven decisions. Start by assessing your current process and determineing areas for improvement, then select the right tools and training to ensure achievementful implementation. Contact us today for a complimentary consultation to discuss how to streamline your fleet maintenance.