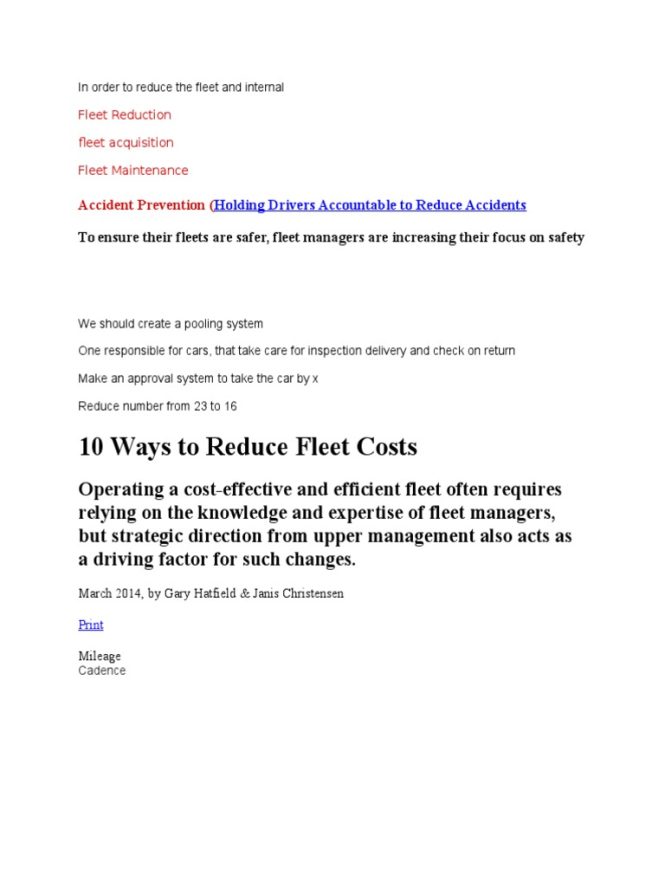
Dealing with unexpected fleet vehicle breakdowns is a common challenge for businesses relying on transportation services. These disruptions can lead to significant financial losses, decreased productivity, and reputational damage. This comprehensive guide dives deep into the strategies for minimizing the impact of these unfortunate events. We’ll explore proactive maintenance measures, effective emergency response protocols, and the crucial role of communication in mitigating downtime and maintaining operational efficiency. We’ll also look at the importance of proper diagnostic tools and spare parts inventory, plus how to establish a safety-first culture to ensure reliable performance. This guide outlines a step-by-step approach for businesses to understand, prevent, and respond to fleet vehicle breakdowns effectively.
Proactive Maintenance Strategies for Minimizing Breakdowns
Implementing Preventative Maintenance Schedules
Preventive maintenance is essential for preventing unexpected breakdowns. A well-structured schedule ensures vehicles are inspected regularly and necessary repairs are performed before problems escalate. This proactive approach minimizes downtime and reduces the chance of catastrophic failure. By investing in comprehensive maintenance programs, fleets can anticipate potential issues and address them before they disrupt operations.
Utilizing Advanced Diagnostic Tools
Advanced diagnostic tools can detect potential issues early, allowing for timely repairs and preventing more significant problems from developing. Real-time monitoring systems can provide insights into vehicle performance, enabling proactive interventions to address potential malfunctions before they lead to breakdowns.
Importance of Regular Inspections and Reporting
Regular inspections are vital for identifying potential problems early on. A documented system for recording inspection findings and maintenance activities can create a clear audit trail, facilitating quick identification of the cause of a breakdown if it does occur. This information also helps anticipate and plan for future preventative maintenance needs.
Effective Emergency Response Protocols
Establishing Clear Communication Channels
Establishing clear communication channels is critical for a swift and coordinated response. A dedicated emergency contact list, along with defined communication protocols, can ensure that necessary information reaches the appropriate personnel promptly during a breakdown. This rapid response is vital for minimizing downtime.
Utilizing a Mobile Repair Team
Consider deploying a mobile repair team equipped with essential tools and parts to address breakdowns at the location. This can significantly reduce the time it takes to repair the vehicle and get it back on the road.
Stockpiling Essential Spare Parts
Maintaining an adequate inventory of essential spare parts can dramatically shorten the time required for repairs. Proactive planning and stock management are essential elements for reducing downtime and ensuring the immediate availability of critical parts.
Safety Protocols and Driver Training
Driver Training for Avoiding Breakdowns
Comprehensive driver training programs can help drivers recognize warning signs of potential breakdowns. Educating drivers about proper vehicle operation and maintenance procedures can help them report issues early, preventing more serious problems. This can also include safety checks and quick maintenance tasks.
Creating a Safety-First Culture
Encouraging reporting of even minor issues and promoting a culture of safety is vital for preventing serious breakdowns. A supportive environment that empowers employees to report potential problems without fear of retribution fosters a more proactive approach to fleet maintenance and safety.
Analyzing Data to Identify Trends
Collecting data on breakdowns, their causes, and repair times helps identify trends and patterns. This analysis can assist in proactive planning, preventive maintenance scheduling, and the prioritization of resources for resolving recurring issues. Identify the frequency of issues for specific vehicle types and adjust the maintenance schedule accordingly.
Minimizing Downtime and Cost Reduction
Calculating the Cost of Downtime
Businesses should analyze the cost of downtime associated with unexpected vehicle breakdowns. Consider the lost revenue, labor costs, and any potential penalties for late delivery. By understanding these figures, companies can prioritize preventative maintenance and emergency response strategies more efficiently.
Utilizing Technology to Monitor and Track
Utilize technology for real-time monitoring and tracking of vehicles. This allows for proactive identification of potential problems and the scheduling of maintenance based on data-driven insights.
Developing a Contingency Plan
Developing a comprehensive contingency plan for unexpected vehicle breakdowns is essential. This plan should outline clear procedures for emergency response, communication, and resource allocation to mitigate the impact of a breakdown and minimize downtime.
Strategies for Communication
Establishing Communication Protocols
Establishing effective communication protocols between drivers, mechanics, and management is essential. This can involve instant messaging systems, email alerts, and regular progress updates to ensure everyone is aware of the situation and the status of the repairs. Real-time information sharing is paramount for efficient problem-solving.
Improving Communication Between Departments
Improved communication between different departments such as maintenance, operations, and logistics ensures everyone is aware of the situation and takes appropriate actions. This collaboration allows for the swift identification and resolution of the breakdown.
Communicating with Customers About Delays
If a breakdown causes delays in deliveries, communicate promptly with customers and provide updates on expected restoration times. This proactive approach helps maintain customer relationships and minimizes negative perceptions.
Dealing with breakdowns efficiently
Effective methods for fast response
Use the following methods to reduce breakdown response time; well-defined communication protocols, a dedicated mobile repair team, and sufficient spare parts. Ensuring your team has the required skills for diagnosis and repair is also essential for swift response and minimize downtime.
The role of mobile repair teams
Incorporate mobile repair teams equipped with essential tools, parts, and expertise to immediately address breakdowns. This can reduce response time and minimize the disruption caused to operations, allowing swift repairs and getting vehicles back on the road quickly.
Impact of advanced diagnostic tools
Advanced diagnostics tools can significantly reduce the length of repairs as they allow for rapid identification of the issue. This will then help mechanics to perform repairs more quickly and effectively. Using real-time monitoring systems is vital as it allows the team to spot problems earlier and take immediate action.
Developing a Breakdown Reporting System
A Clear and Concise Breakdown Reporting System
Develop a structured breakdown reporting system for fleet vehicles. This system should include a standardized reporting template encompassing the details of the breakdown (date, time, location, vehicle identification number, nature of the breakdown, reported by). This data collection is crucial for identifying patterns and improving maintenance strategies.
Using Technology to Track and Report
Employ technology to automate the breakdown reporting system. This can streamline the process, ensuring accurate and timely data input. This could involve mobile apps for drivers and a central dashboard for management.
Analyze Breakdown Data
Analyzing the data gathered from the breakdown reporting system can provide valuable insights into the patterns and causes of breakdowns. This data can support decisions on preventative maintenance, spare part inventory management, and training programs.
Managing Spare Parts Effectively
Establishing an Inventory Management System
A well-maintained spare parts inventory can dramatically reduce the time it takes to repair vehicles. Implement a systematic inventory management system to track the stock of critical spare parts, ensuring timely replenishment. Track usage patterns to anticipate future needs.
Building a Culture of Safety and Communication
Employee Training for Safety
Train drivers on how to avoid potential hazards and identify warning signs of vehicle issues. Safety training is critical for maintaining a culture of safety within the fleet. Training can be done through workshops, online resources, or hands-on practical sessions.
Encourage Reporting of Potential Issues
Foster a supportive work environment where drivers feel comfortable reporting potential issues. Establish a clear reporting process so that problems are addressed before they escalate.
Regular Safety Audits
Implement regular safety audits to evaluate fleet safety procedures and identify any potential improvement areas. Regular audits ensure compliance with safety standards and promote a consistent safety culture within the fleet. This proactive safety approach protects personnel and ensures smooth fleet operation.
In conclusion, effectively dealing with unexpected fleet vehicle breakdowns is crucial for maintaining operational efficiency and minimizing financial losses. By implementing proactive maintenance schedules, investing in robust diagnostic tools, and fostering a culture of safety and communication, companies can significantly reduce the impact of these disruptions. Our comprehensive guide has provided you with actionable strategies and insights. To avoid similar incidents and for tailored fleet management solutions, contact us today for a consultation.