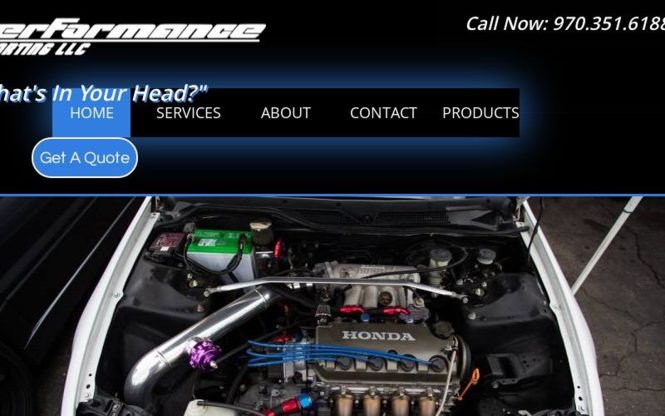
Dealing with quality issues in aftermarket detailing products is a critical challenge for companies in the industry. A single flawed product can severely damage a company’s reputation and erode customer trust. Aftermarket detailing products, often sold through various channels like online stores and retail partners, are particularly susceptible to quality issues stemming from supply chain disruptions, manufacturing errors, or improper storage. This article explores effective strategies for identifying, diagnosing, and resolving quality problems in aftermarket detailing products, ultimately ensuring customer satisfaction and preserving a positive brand image. It will delve into preventative measures, complaint handling procedures, and how to learn from errors to avoid future issues. The structure of this article is as follows: first, we will define the problem and outline the challenges; second, we will explore preventative measures, such as quality control protocols; third, we will detail procedures to address customer complaints; and finally, we will discuss the conclusion, which includes recommendations for the future and recommendations to avoid future similar issues.
Identifying the Root Cause of Quality Issues
Understanding the complexities of Aftermarket Detailing
The aftermarket detailing product market is vast and complex, with a wide array of products, manufacturers, and retailers involved. This complexity can make it challenging to pinpoint the exact cause of quality issues. Many factors contribute to quality problems, from supplier reliability to manufacturing processes and even customer misuse or storage issues. Therefore, a thorough analysis is required to identify the root causes and implement effective solutions. This involves diligent investigation, including feedback from customers, reviews from retailers, and analysis of product samples to determine the root of the problem, whether it’s raw material inconsistencies, manufacturing defects, or inconsistencies in quality control procedures.
Common Causes of Quality Problems
Common causes of quality issues include faulty raw materials, inadequate manufacturing processes, inconsistent quality control, inappropriate storage conditions, and issues in the supply chain. The use of sub-par materials and components directly impacts the final product quality, leading to a decline in performance and overall satisfaction. Furthermore, poorly managed quality control protocols within manufacturing processes can result in imperfections or defects passing unnoticed, creating quality problems in finished goods. Similarly, inappropriate storage environments, insufficient testing, and issues during shipping all contribute to the likelihood of product defects and customer dissatisfaction.
Implementing Proactive Quality Control Measures
Robust Quality Control Procedures
Implementing robust quality control procedures from the initial raw material selection to the final product inspection is paramount. This involves establishing clear standards, rigorous testing procedures, and transparent communication across the supply chain. Comprehensive quality checks at each stage can minimize the production of faulty products and identify potential problems before they reach consumers. Careful monitoring of production processes and quality control protocols ensures that all products meet the defined standards, minimizing the probability of defective products entering the market.
Monitoring and Analysis of Customer Feedback
Monitoring and analyzing customer feedback is essential to detect emerging quality issues early. Customer reviews, complaints, and return rates provide valuable insights into product performance and potential problems. By analyzing these feedback mechanisms, manufacturers and retailers can pinpoint specific problems and react swiftly. Tracking these data points helps them understand the root causes of the problems, implement necessary improvements, and increase the overall satisfaction of their consumers. Regular analysis of customer feedback and return data enables proactive improvement and prevention of future problems.
Addressing Customer Complaints Effectively
Establishing a Clear Complaint Handling Process
A well-defined complaint handling process is critical to resolving customer issues efficiently. This includes establishing clear communication channels, promptly acknowledging complaints, and offering appropriate solutions. When responding to customer complaints, it’s essential to exhibit empathy and resolve the issue quickly. Providing a timely and satisfactory resolution demonstrates a commitment to customer satisfaction and builds trust in the brand.
Offering Solutions and Following Through
Once a complaint is received, offering a prompt and satisfactory solution is critical. This might include a full refund, a replacement product, or other appropriate compensation. Following up with customers after addressing their concerns is also important to ensure that the issue is resolved effectively and avoid future issues. Regular follow-ups and consistent communication reinforce the brand’s commitment to customer satisfaction and contribute to maintaining a positive reputation.
Preventing Future Quality Issues
Continuous Improvement and Learning from Mistakes
Continuous improvement is essential to prevent recurring quality issues. A company should analyze past problems and learn from each mistake to develop more effective preventative measures in the future. Learning from failures is crucial for future success and growth; it requires proactive analysis of past mistakes, identification of trends, and development of new strategies for error reduction.
Using Data Analysis to Identify Trends
Utilizing data analysis to identify patterns and trends in quality issues is vital. Statistical analysis of return rates, customer complaints, and internal defect rates can highlight recurring issues. Identifying these trends is vital in avoiding repetitive quality problems and improving the products and processes to create better products.
Long-Term Strategies for Maintaining Quality
Investing in Quality Management Systems
Investing in comprehensive quality management systems can enhance long-term quality. This involves adopting standardized processes, implementing quality control tools, and training employees. By establishing quality management systems, companies create a comprehensive framework for preventing, detecting, and correcting quality issues. These systems not only ensure high-quality products but also foster a culture of continuous improvement, promoting customer satisfaction and protecting the company’s reputation.
Building Strong Relationships with Suppliers
Building strong relationships with suppliers is critical. This will enable effective communication regarding product specifications, quality standards, and potential challenges. A cooperative approach to quality management fosters transparency and mutual understanding, minimizing the risk of quality issues arising from the supply chain. Strong supplier partnerships allow for shared knowledge, proactive communication, and a collective commitment to producing high-quality products.
Q: How can companies effectively prevent quality issues from recurring in aftermarket detailing products?
A: Companies can prevent recurring quality issues in aftermarket detailing products by implementing a proactive quality control system that includes rigorous testing procedures, inspecting all products for defects, establishing clear communication channels, and improving the supply chain. They should also collect and analyze customer feedback, address complaints swiftly and thoroughly, and continuously evaluate processes to identify and eliminate areas prone to quality problems. By prioritizing preventative measures and learning from past mistakes, companies can significantly reduce the frequency of recurring quality issues.
In conclusion, effectively handling quality issues in aftermarket detailing products is crucial for maintaining customer satisfaction and brand reputation. By implementing proactive quality control measures, promptly addressing complaints, and consistently improving processes, companies can minimize costly returns, avoid reputational damage, and foster long-term customer loyalty. For further assistance, consider consulting with quality assurance experts or exploring available resources for quality management. Take immediate action to prevent issues from escalating. Implement a robust quality control system and address any issues immediately.