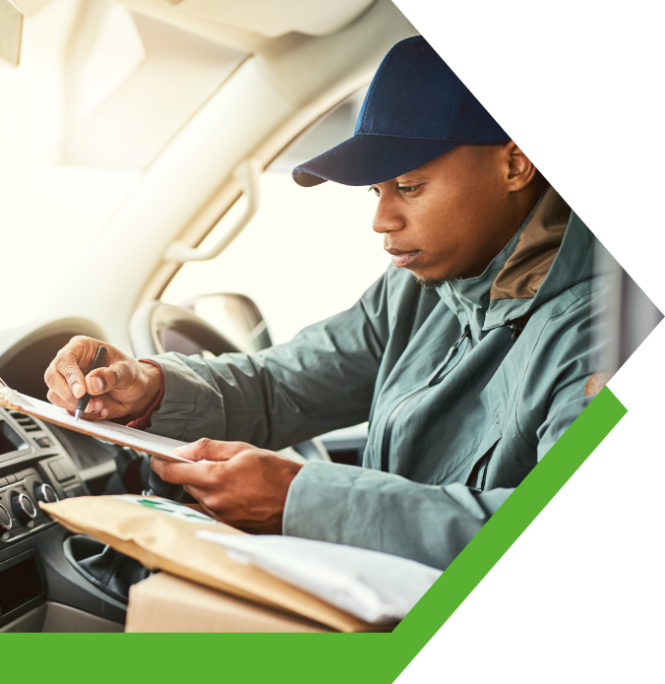
Implementing a preventative maintenance plan for your business vehicles is a crucial step towards optimizing fleet performance and minimizing costly downtime. A well-structured plan can dramatically improve the lifespan of your vehicles, enhance driver safety, and save you significant money on repairs. This article explores the key components of a successful preventative maintenance plan, outlining how you can implement and manage one effectively. We’ll discuss the benefits of proactive maintenance, highlight common issues and solutions, and offer a practical framework for integrating a preventive maintenance plan into your daily operations. This comprehensive guide will walk you through each stage, ensuring you have a solid foundation for creating a tailored preventative maintenance plan for your specific business needs.
Understanding the Importance of Preventative Maintenance
Defining Preventative Maintenance
Preventative maintenance is a proactive approach to vehicle upkeep. Rather than reacting to breakdowns, you schedule routine inspections, replacements, and repairs to prevent future issues. This approach can significantly reduce unexpected downtime, saving you money and time. By focusing on the long-term health of your vehicles, you’re investing in a sustainable and profitable fleet management strategy.
The Business Case for Preventative Maintenance
Studies consistently show that companies with robust preventative maintenance programs experience fewer breakdowns, decreased repair costs, and increased vehicle lifespan. The savings from avoiding unexpected repairs often exceed the cost of implementing the plan. A proactive approach to fleet maintenance, rather than a reactive one, helps to minimize downtime and maximize the return on investment for your fleet. Consider an example of a company with 10 vehicles. An average of one vehicle being out of service per week can have a huge impact on productivity, scheduling, and overall operational costs. The cost of vehicle downtime can vary widely, but a conservative estimate could range from $500 to $2000 per day per vehicle.
Creating a Comprehensive Preventative Maintenance Schedule
Developing a Detailed Maintenance Checklist
A key component of a successful preventative maintenance plan is a well-defined maintenance checklist. This document should outline all the tasks, parts, and intervals for each vehicle. It should include things like oil changes, tire rotations, fluid checks, brake inspections, and filter replacements. Include specific procedures and parts required for each task, as well as the corresponding time intervals. A robust maintenance checklist will serve as the cornerstone of your preventative maintenance program, ensuring that every crucial element is addressed and tracked effectively.
Utilizing Technology for Enhanced Tracking
Employing fleet management software and maintenance tracking apps can significantly streamline the process. Software allows for digital record-keeping of all maintenance activities, ensuring that information is organized and readily available. Furthermore, some software applications even provide notifications and alerts, prompting you about upcoming maintenance tasks and ensuring that nothing is missed. This can save considerable time and effort in managing your fleet’s maintenance schedule and records.
Implementing and Managing the Preventative Maintenance Plan
Training Your Maintenance Team
Properly trained staff are crucial for successful implementation. Your technicians and drivers need to understand the procedures outlined in the maintenance checklist. Regular training sessions, demonstrations, and clear communication are essential. Ensuring staff possess the knowledge and skills to execute the preventative maintenance tasks correctly is vital to prevent errors and ensure quality work.
Regular Inspections and Documentation
Regular inspections are critical for identifying potential problems early on. This approach enables addressing small issues before they escalate into major breakdowns. Maintain a detailed log of every maintenance activity, including the date, time, nature of the work, parts used, and technicians involved. Thorough documentation ensures accurate tracking of maintenance history, supporting informed decision-making and providing a record for future reference. This is especially helpful when resolving warranty claims or assessing vehicle performance over time.
Addressing Specific Vehicle Maintenance Needs
Addressing Different Vehicle Types
Preventative maintenance procedures vary based on the type of vehicle. Trucks, buses, and cars have different maintenance requirements. For example, trucks need more frequent oil changes and tire rotations than cars. Develop specific maintenance checklists for each type of vehicle in your fleet, taking into account its unique needs and usage patterns. This personalized approach will ensure the plan aligns perfectly with your specific vehicle types and usage.
Seasonal Variations in Maintenance
Weather conditions significantly impact vehicle maintenance. For instance, winter conditions demand additional attention to antifreeze levels and tire pressure, while summer heat requires vigilance regarding cooling systems and air conditioning. Incorporate seasonal variations in your maintenance schedule to address potential issues.
Optimizing Fleet Efficiency Through Preventative Maintenance
Minimizing Downtime and Maximizing Uptime
Implementing preventative maintenance directly impacts your fleet’s efficiency. By addressing issues proactively, you minimize the likelihood of unexpected breakdowns and maintain a high level of uptime. This ensures that your vehicles are consistently available for use, contributing to operational efficiency and productivity. The result is streamlined operations and a significant boost in overall profitability.
Reducing Repair Costs and Extending Vehicle Lifespan
Preventative maintenance significantly reduces the cost of repair and maintenance. Instead of dealing with costly breakdowns, you’re addressing small issues before they escalate. Proactive maintenance extends the lifespan of your vehicles, resulting in fewer replacement expenses and ensuring maximum utilization. The combination of reduced repair costs and increased lifespan allows for significant long-term financial gains.
Tracking Performance and Making Adjustments
Analyzing Data for Optimization
Regularly monitor and analyze the data collected from your preventative maintenance program. Identify patterns, trends, and areas for improvement. Is there a specific component that is failing more frequently than expected? Utilize this information to refine your schedule and prioritize maintenance tasks.
Refining the Maintenance Schedule
Based on the analysis, adjust the maintenance schedule as needed. Consider adding more frequent inspections or maintenance tasks for components identified as having high failure rates. A flexible and adaptable approach allows you to modify the plan as your fleet’s needs evolve, leading to maximum efficiency and minimizing costly disruptions.
Examples of Preventative Maintenance for Specific Vehicles
Preventative Maintenance for Light-Duty Trucks
For light-duty trucks, regular oil changes are essential, along with routine tire rotations, and inspections of brake pads and fluids. Check the air filter, fuel filter, and coolant levels at prescribed intervals to maintain optimal performance. Additionally, inspect the lights and indicators regularly to avoid unexpected failures.
Preventative Maintenance for Heavy-Duty Trucks
Heavy-duty trucks require more comprehensive maintenance schedules. This includes daily driver inspections, more frequent oil changes, regular inspection of the transmission and drivetrain, and meticulous monitoring of tire pressure and tread depth.
Conclusion (repeated): (same as above)
FAQ:
What are some common pitfalls in preventative maintenance programs?
“Common pitfalls in preventative maintenance programs often stem from inadequate planning, lack of proper training, and inconsistent execution. Failing to track maintenance data effectively can also hinder optimization. Inconsistent documentation or neglecting to address small issues early on can lead to substantial problems. To avoid these pitfalls, start with a clear plan, providing thorough training to all staff involved. Consistent follow-up and documentation are vital for refining your program over time.
How do I prioritize maintenance tasks for my fleet?
Prioritizing maintenance tasks for your fleet requires a careful evaluation of your vehicle usage patterns, the history of previous issues, and the current condition of each vehicle. Consider using a risk assessment methodology to analyze the potential consequences of component failures. A comprehensive approach will help you identify critical components and assign a priority level for maintenance procedures. Use your data and the knowledge of your team to make the most efficient decisions.
What is the ROI of implementing a preventive maintenance program?
The return on investment for a preventive maintenance program is substantial. Reduced repair costs, minimized downtime, and extended vehicle lifespans directly translate to significant financial savings. Beyond the financial benefits, consider the positive impact on driver safety and the improved reliability of your fleet. When properly executed, these factors can enhance business operations, contributing positively to your overall bottom line.
In conclusion, implementing a preventative maintenance plan for business vehicles is crucial for maximizing uptime, reducing repair costs, and ensuring driver safety. By following these steps and incorporating the preventative maintenance plan into your daily operations, you can significantly enhance your fleet’s operational efficiency and profitability. Schedule a consultation with a fleet management specialist today to discuss a tailored preventative maintenance plan for your specific needs. This consultation will provide invaluable insights and guidance on optimizing your preventative maintenance strategies and maximizing your fleet’s performance.